Format: Multiple Choice
Duration: 90 Minutes
Number of Questions: 50
Passing Score: 68%
Validation: This exam has been validated against 23A/23B/23C/23D/24A/24B.
Policy: Cloud Recertification
Earn associated certifications
Passing this exam is required to earn these certifications. Select each certification title below to view full requirements.
Oracle Manufacturing Cloud 2024 Certified Implementation Professional
Examkingdom Oracle 1Z0-1075-24 Exam pdf
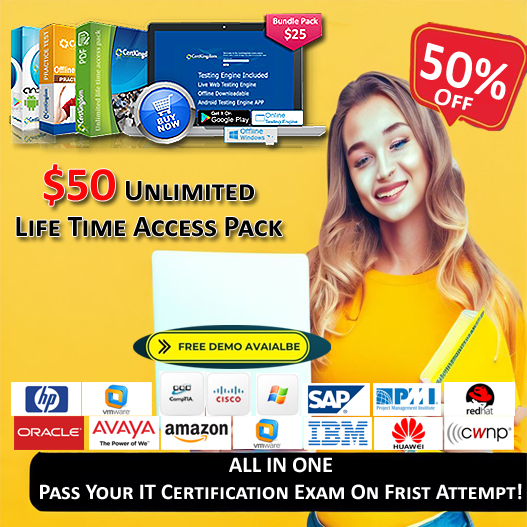
Best Oracle 1Z0-1075-24 Downloads, Oracle 1Z0-1075-24 Dumps at Certkingdom.com
Prepare to pass exam: 1Z0-1075-24
An Oracle Manufacturing Cloud 2024 Certified Implementation Professional has demonstrated the knowledge and skills required to use Oracle Manufacturing Cloud on a project by creating work orders, managing work definitions, and executing production. Individuals who earn this certification are able to set up Manufacturing, set up reporting and analytics and understand the complexities of manufacturing integrations, including Costing and Inventory foundations.
If you have a valid Oracle Manufacturing Cloud Implementation Professional Certification, and your credential has not expired, you can maintain your certification by taking the corresponding shorter Delta exam.
Check the Oracle Recertification Policy to see if you qualify.
Take recommended training
Complete one of the courses below to prepare for your exam (optional):
Become a Certified Manufacturing Implementer
Additional Preparation and Information
A combination of Oracle training and hands-on experience (attained via labs and/or field experience), in the learning subscription, provides the best preparation for passing the exam.
Review exam topics
Setting up Manufacturing Elements
Summarize the key features of Functional Setup Manager and Simplified Setup
Set up common configuration elements
Configure Resources, Operations, and Work Centers
Set up Plant Parameters and Security, Profile Options, Lookups and DFFs
Manage Production Calendars and add Shift and Work Center Resource exceptions
Managing Work Definitions
Create a work definition
Calculate manufacturing lead time
Process the item structure changes
Create work definition versions
Generate work definitions automatically
Manage items and structures
Managing Work Orders
Identify the key functionalities in Work Execution Work Areas
Create and update work orders for standard and non-standard work orders and serialized manufacturing
Analyze Work Order Reservations and History
Executing Production
Summarize the key features of Production Execution transactions including Outside Processing
Identify the key functionalities in Dispatch List
Report production transactions
Report orderless transactions
Analyze Production Transaction Review and Product Genealogy
Transfer production transactions to costing
Import production transactions
Create, manage, and resolve manufacturing production exceptions
Integrating Manufacturing Modules
Identify the key functionalities of Manufacturing Cloud integrations
Manufacturing Costing
Identify the key functionalities of Production Costs
Evaluate Work Order Completion Cost including Partial and Scrap
Summarize the key features of Cost Reporting including WIP Inventory Valuation Report
Set up and implement Cost Planning estimates
Using Reporting and Analytics for Manufacturing
Execute Basic Transaction and Work Order Reporting
Set up BI Reporting and OTBI
Costing and Inventory Foundations
Outline common inventory configurations
Identify the key functionalities of Managerial Accounting Basics and Cost Accounting
Managing Projects Enabled SCM
Outline the common projects enabled SCM configurations
Manage project enabled work orders
Sample Question and Answers
QUESTION 1
Which three statements are true about managing Units of Measure?
A. You must define the unit of measure class with a base unit of measure.
B. If you want to transact items in units of measure that belong to classes other than their primary UOM class, you must define conversions between the base units of measure in different UOM classes.
C. A unit of measure standard conversion specifies the conversion factor by which the unit of measure is equivalent to the unit of measure class.
D. Conversions between classes are unique for each item; the conversion rate varies for intraclass units of measure.
E. A unit of measure conversion is a mathematical relationship between two different units of measure.
Answer: ABE
Explanation:
In Oracle Manufacturing Cloud, managing Units of Measure (UOM) is critical to ensuring that
transactions, measurements, and conversions are handled accurately. Below is a detailed explanation of the correct statements:
Statement A: You must define the unit of measure class with a base unit of measure “ This is a
fundamental setup in Oracle Manufacturing Cloud. Every UOM class must have a base unit of
measure defined because it serves as the reference for all conversions within the class. The base
UOM acts as a standard, and all other UOMs within the class are defined relative to it.
Reference: Oracle Fusion SCM: “Units of Measure Setup” documentation explains the importance of
defining a base unit for every UOM class for system consistency and accurate conversions.
Statement B: If you want to transact items in units of measure that belong to classes other than their
primary UOM class, you must define conversions between the base units of measure in different
UOM classes “ This is true. If an items UOM belongs to one class, but you need to transact in
another UOM from a different class, a conversion must be defined between the base UOMs of the
two classes. This ensures seamless inter-class transactions and measurement consistency.
Reference: Oracle Cloud SCM Common Setup Guide for “Units of Measure Conversion” states that
cross-class UOM transactions require conversion definitions for operational accuracy.
Statement E: A unit of measure conversion is a mathematical relationship between two different
units of measure “ UOM conversions in Oracle Cloud are defined mathematically, typically by
specifying a conversion factor. This relationship is used by the system to automatically convert
quantities between different units of measure, whether for inter-class or intra-class conversions.
Reference: Oracle Fusion Cloud SCM Documentation on “UOM Conversions” explains that a
mathematical formula or factor is needed to establish the relationship between two UOMs, enabling
transactions across different UOMs.
Incorrect Statements:
Statement C: A unit of measure standard conversion specifies the conversion factor by which the unit
of measure is equivalent to the unit of measure class “ This statement is incorrect because a standard
conversion relates two UOMs directly, not between a UOM and the class itself. Conversions operate
between specific UOMs, not between a UOM and its class.
Statement D: Conversions between classes are unique for each item; the conversion rate varies for
intraclass units of measure “ This is not accurate because conversions between UOM classes are not
unique for each item. Once a UOM conversion is established between classes, it applies globally
unless there are specific item-level conversions.
This ensures a consistent approach to defining, transacting, and converting units of measure across
different manufacturing and inventory processes within Oracle Manufacturing Cloud.
QUESTION 2
Which three statements are true about the main areas of Managerial Accounting?
A. Receipt Accounting Is the application that performs accrual accounting for all types of receipts.
B. Landed Cost Management gives organizations financial visibility into their extended supply chain costs.
C. Supply Chain Orchestration automatically selects the correct process based on user-defined Subledger Accounting rules when a supply creation Is initiated.
D. Cost method can be defined with granularity down to individual Items.
Answer: ABD
Explanation:
In Oracle Manufacturing Cloud and related financial applications, managerial accounting plays a
significant role in tracking and managing costs across supply chain and manufacturing activities. The
following is a breakdown of the correct statements:
Statement A: Receipt Accounting is the application that performs accrual accounting for all types of
receipts “ Receipt Accounting is a crucial module in Oracle Cloud that supports the tracking of costs
and performs accruals related to receipts. This includes processes such as procurement receipts,
interorganization transfers, and supplier shipments. This allows organizations to recognize and
account for the expenses associated with these receipts.
Reference: Oracle Cloud SCM Documentation for Receipt Accounting outlines how the system
manages accruals and matches them with purchase orders and invoices.
Statement B: Landed Cost Management gives organizations financial visibility into their extended
supply chain costs “ Landed Cost Management is designed to capture additional costs that arise
during the transportation, handling, and processing of goods. This includes costs like shipping,
insurance, and customs duties. By including these in the overall cost, it provides a more
comprehensive view of the actual costs of goods in the supply chain.
Reference: Oracle Fusion SCM Guide, “Landed Cost Management,” describes how it aggregates
various indirect supply chain costs to give better financial visibility.
Statement D: Cost method can be defined with granularity down to individual items “ In Oracle
Manufacturing Cloud, costing methods can be assigned not only at the organization level but also at
a granular level down to individual items. This provides flexibility in defining different costing
strategies for different products depending on their nature, manufacturing process, or market conditions.
Reference: Oracle Manufacturing Cloud User Guide explains the flexibility in configuring cost
methods at different organizational and item-specific levels.
Incorrect Statements:
Statement C: Supply Chain Orchestration automatically selects the correct process based on userdefined
Subledger Accounting rules when a supply creation is initiated “ While Supply Chain
Orchestration automates various supply chain processes, it does not select processes based on
Subledger Accounting rules. The orchestration system is more focused on managing and coordinating
supply chain processes rather than determining accounting rules.
QUESTION 3
Which three are Cost accounting methods’
A. Perpetual Average Cost
B. Layer Cost, also known as “LIFO”
C. Frozen Standard Cost
D. Actual Cost, also known as “FIFO”
E. Periodic Actual Cost
Answer: A, C, D
Explanation:
Oracle Manufacturing Cloud supports multiple cost accounting methods to help organizations track
the cost of their goods and inventory effectively. Below is an explanation of the correct answers:
Statement A: Perpetual Average Cost “ This is a commonly used method in Oracle Cloud where the
system continuously updates the average cost of an item with each receipt or transaction. This
method is useful for organizations that need to track the moving average cost of goods in real-time.
Reference: Oracle SCM Cloud Cost Management Guide explains how Perpetual Average Cost is
maintained and updated across transactions.
Statement C: Frozen Standard Cost “ This method involves predefining a standard cost for each item
at the beginning of a financial period. The cost remains “frozen” throughout the period, and
variances between the actual cost and the standard cost are tracked and analyzed separately.
Reference: Oracle Costing Methods documentation specifies that the Frozen Standard Cost method is
particularly useful for manufacturers who need stable cost inputs over a financial period.
Statement D: Actual Cost, also known as “FIFO” “ The FIFO (First In, First Out) method records costs
based on the order in which items are received. It is a type of actual costing where items are valued
based on the specific costs of the earliest received inventory. Oracle Cloud supports FIFO as part of its actual costing methods.
Reference: Oracle Cost Accounting documentation details the use of FIFO for tracking actual costs in a layered costing approach.
Incorrect Statements:
Statement B: Layer Cost, also known as “LIFO” “ Oracle Cloud does not natively support LIFO (Last In,
First Out) as a cost method due to accounting and regulatory restrictions in various regions. LIFO is
generally not used in the system as a standard method.
Statement E: Periodic Actual Cost “ While there is a method called Periodic Average Cost, Periodic
Actual Cost is not typically listed as a standard costing method in Oracle Cloud.
QUESTION 4
You are implementing project-driven supply chain functionality. You need to set up movement
requests to issue or transfer project material to manage the inventory associated with projects and tasks.
Which two are types of movement requests to issue or transfer project material?
A. Transfer project material from one subinventory to another.
B. Pick transactions Interfaced by the project costing project and task using the project material, common Inventory, or Inventory from another project.
C. Create o movement receipt line with the Project Costing widget.
D. Perform manual pick for such movement requests using the project material, common inventory, or inventory from another project.
Answer: A, D
Explanation:
When setting up movement requests in a project-driven supply chain, you need to manage inventory
associated with specific projects and tasks. The two correct types of movement requests in this context are:
Statement A: Transfer project material from one subinventory to another “ This is a standard type of
movement request in Oracle Cloud, allowing project materials to be transferred between
subinventories. It is essential for managing inventory tied to specific projects and tasks, ensuring that
materials are available where needed for project execution.
Reference: Oracle Fusion SCM Cloud: Inventory Management Guide describes how material transfers
can be executed between subinventories, including project-based transfers.
Statement D: Perform manual pick for such movement requests using the project material, common
inventory, or inventory from another project “ Manual picking for project-specific material is another
supported operation. It allows users to perform manual picks from various sources, such as project
material, common inventory, or even inventory from other projects.
Reference: Oracle Project-Driven Supply Chain documentation explains how manual picks can be
configured to source inventory based on project requirements.
Incorrect Statements:
Statement B: Pick transactions are not interfaced specifically by project costing. Although project
costing is relevant for tracking costs, it is not the driving factor behind pick transactions.
Statement C: There is no concept of creating a movement receipt line with the “Project Costing
widget” in Oracle Manufacturing Cloud.
QUESTION 5
In which three ways does Supply Chain Orchestration enrich supply requests with project details to support outside processing for a project-specific work order?
A. Supply Chain Orchestration initiates the creation of a purchase order without the work order.
B. Expenditure Item Date Is set to the requested need-by date and Expenditure Organization is set to the manufacturing plant.
C. Expenditure Item Date is set to the receipt date and Expenditure Organization is set to the manufacturing plant.
D. Supply Chain Orchestration initiates the creation of a requisition with the project details.
E. Expenditure Type is sat to the expenditure type associated to the outside processing Item.
Answer: B, D, E
Explanation:
Supply Chain Orchestration (SCO) plays a vital role in managing project-specific work orders,
particularly for outside processing. Heres how it enriches supply requests with project details:
Statement B: Expenditure Item Date is set to the requested need-by date and Expenditure
Organization is set to the manufacturing plant “ In project-specific work orders, Supply Chain
Orchestration assigns the need-by date as the Expenditure Item Date. The Expenditure Organization
is typically set to the manufacturing plant handling the work order.
Reference: Oracle Fusion Project-Driven Supply Chain documents this behavior, showing how
expenditure details are linked to the project for costing purposes.
Statement D: Supply Chain Orchestration initiates the creation of a requisition with the project
details “ SCO automatically creates a requisition with all relevant project details, such as project
number, task, and expenditure information. This ensures that the procurement process is aligned
with the projects financial and material requirements.
Reference: Oracle SCM Cloud Supply Chain Orchestration User Guide details the automated creation
of requisitions with project data for external processing.
Statement E: Expenditure Type is set to the expenditure type associated with the outside processing
item “ In Oracle Cloud, expenditure types must align with the specific processing items. SCO ensures
that the correct expenditure type is applied to the work order and subsequent requisitions.
Reference: Project Financial Management guides in Oracle SCM Cloud explain how expenditure types
are associated with items, ensuring accurate costing.
Incorrect Statements:
Statement A: SCO does not initiate the creation of a purchase order without the work order. A work
order is essential for processing the outside work, and its absence would disrupt the orchestration process.
Statement C: The Expenditure Item Date is not set to the receipt date but rather to the requested
need-by date for proper alignment with project scheduling.
Post your comments